22. Gearring Design¶
Ready-to-use parametric gearring design (a.k.a. annulus).
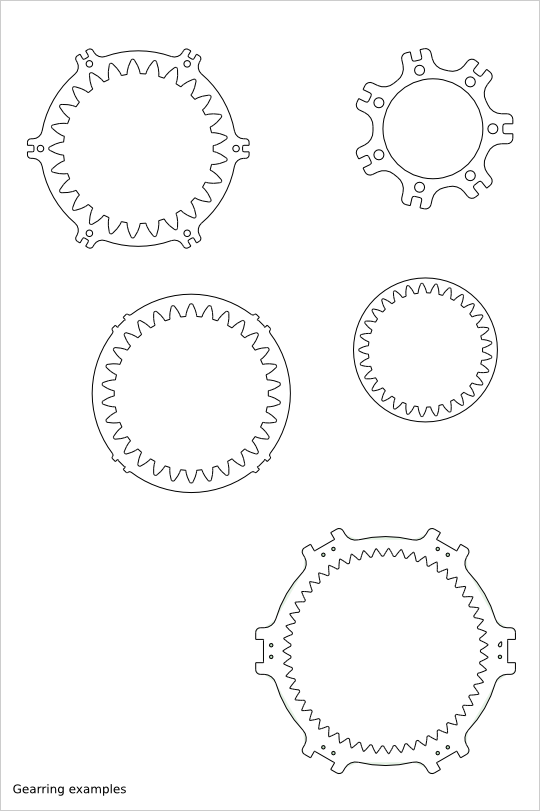
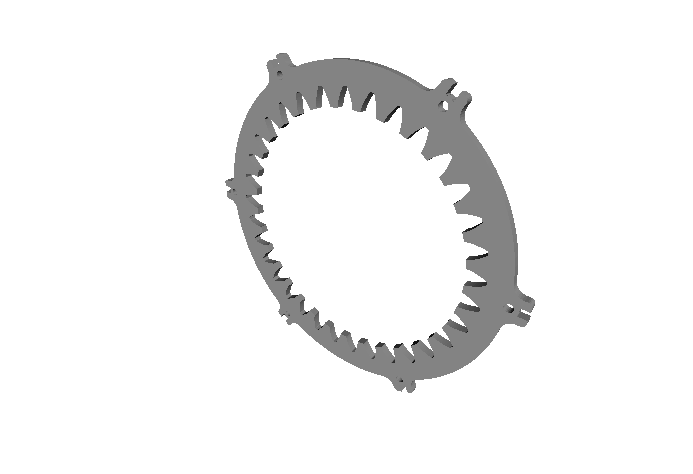
To get an overview of the possible gearring designs that can be generated by gearring(), run:
> python gearring.py --run_self_test
22.1. Gearring Parameter List¶
The parameter relative to the gear-profile are directly inherit from the Gear Profile Function.
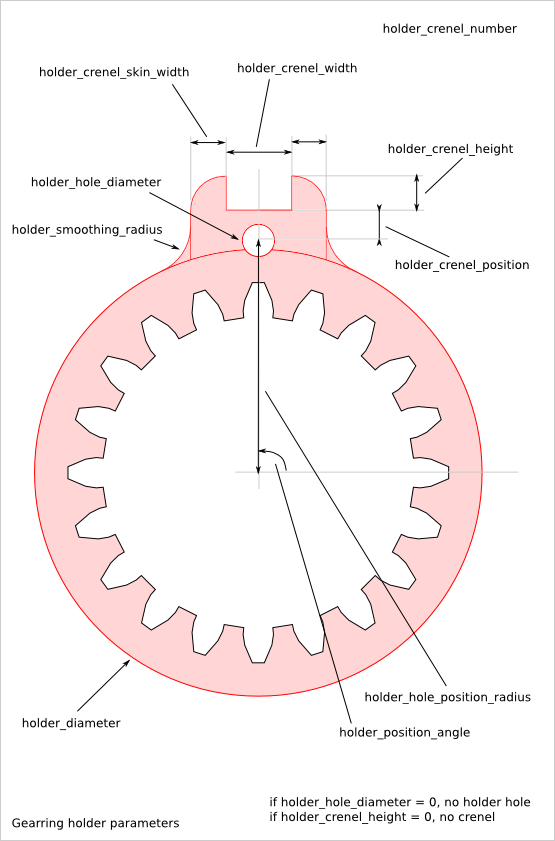
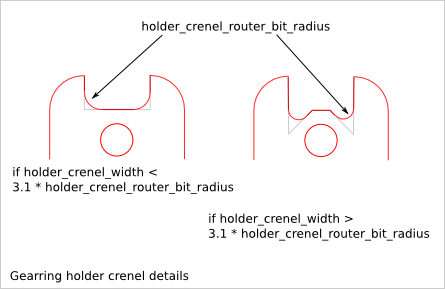
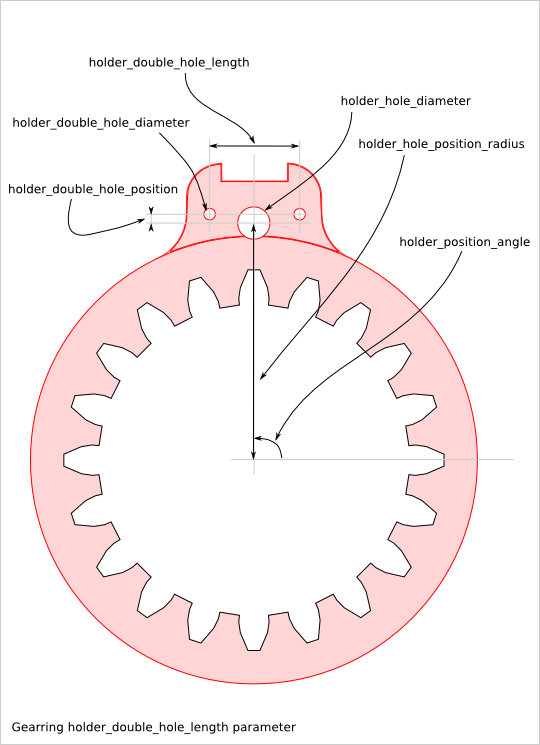
22.2. Gearring Parameter Dependency¶
22.2.1. router_bit_radius¶
Four router_bit radius are defined: gear_router_bit_radius, holder_crenel_router_bit_radius, holder_smoothing_radius and cnc_router_bit_radius. Each set the router_bit radius for different areas except cnc_router_bit_radius that set the minimum value for the three other router_bit radius. If an other router_bit radius is smaller than cnc_router_bit_radius, it is set to cnc_router_bit_radius. So, we have the relations:
cnc_router_bit_radius < gear_router_bit_radius
cnc_router_bit_radius < holder_crenel_router_bit_radius
cnc_router_bit_radius < holder_smoothing_radius
If you leave holder_smoothing_radius to 0.0, it will be changed automatically to the biggest possible value.
22.2.2. holder_hole_diameter¶
holder_hole_diameter sets the diameter of the holder-holes. If holder_hole_diameter is set to 0.0, no holder-hole are created.
22.2.3. holder_crenel_number¶
holder_crenel_number sets the number of holder-crenels (equal to the number of holder-hole). If holder_crenel_number is set to zero, no holder-crenel is created and the outline of the gearring is a simple circle.
22.2.4. holder_crenel_width¶
holder_crenel_width must be bigger than the router_bit diameter:
holder_crenel_width > 2 * holder_crenel_router_bit_radius
If holder_crenel_width is big enough, the crenel bottom shape is changed to get alternative enlarged corners.
22.2.5. gear_tooth_nb¶
gear_tooth_nb sets the number of teeth of the gear_profile. If gear_tooth_nb is set to zero, the gear_profile is replaced by a simple circle of diameter gear_primitive_radius.
22.2.6. Alignment angles¶
gear_initial_angle sets the angle between the X-axis and the middle of the addendum of the first tooth. holder_position_angle sets the angle between the X-axis and the middle of the first holder-crenel. Use gear_initial_angle or holder_position_angle or both to ajust the offset angle between the gear-profile anf the gearring-holder.
22.2.7. holder_hole_mark_nb¶
holder_hole_mark_nb lets you modify the first (or the several first) crenel to help you recognizing the first tooth. The first crenels have a egg-form instead of the circle-form. If you don’t want to mark the first crenel, set crenel_mark_nb to zero. This feature is useful when you need pile up gearring and find easily the first tooth to align them.
22.2.8. holder_double_hole¶
In addition to the holder_hole, you can generate the holder_double_hole defined by the parameters holder_double_hole_diameter, holder_double_hole_length and holder_double_holde_position. The distance between the two double_holes is set by holder_double_hole_length. The radius position is set by holder_double_holde_position relative to the holder_hole_position_radius. The holder_double_holes are useful when you use the crenel-hole with thin steel-rod for alignment and Z-shearing resistance and you want to increase the stability. At the same time, you can use the holder_holes to put threaded rods.